行波管螺旋线的光学检测方法
下载: 973次
1 引言
行波管(TWT)是一种常见的电真空器件,它的基本原理是通过电子注与高频电磁波的互作用,将电子注的能量交给高频电磁波,使高频电磁波得到放大[1]。互作用的基本条件是电子注与高频电磁波速度一致,然而实际电子是无法加速到光速的,需要设计特别的金属导体结构将电磁波的传播速度降低,故各种行波管慢波结构应运而生,如螺旋线、耦合腔、折叠波导、微带曲折等[2],其中形状酷似一根弹簧的螺旋线慢波结构,具有高增益、大功率和宽频带的特点,且制造工艺相对简单,已取得了广泛的应用。
广大国内外学者对其进行深入的研究后发现,互作用过程中,交出部分能量的电子注速度降低,如果电磁波继续在均匀螺距的螺旋线上传输,将不能满足互作用的同步条件,导致互作用效率降低。此外,宽带行波管的频带内往往包含一些噪声信号,如低频段的二次谐波,如果不进行有效的抑制,则会被互作用的过程放大,进而影响输出稳定性。为了解决这些问题,人们发展了螺距渐变、跳变,螺旋线外径带锥角等方法,理论分析、模拟仿真与实测结果都表明采用这些方法效果显著[3-9]。然而,上述异形螺旋线的发展给零件的检测带来了巨大的挑战。在加工制备过程中,为了保证电子效率、同步电压、二次谐波等设计指标,以及装配过盈量[10]、散热系数、力学强度等工艺指标,众多几何要素都成为了全检项目。螺旋线结构脆弱、摆放与调整困难、几何要素测量精度要求高,要实现其精确快速的检测还有许多问题需要解决[11]。其中测量效率低、测量结果不稳定、测量项不足仍是当前存在的主要问题。此外,随着卫星在侦察、通信、导航、测地等领域的大规模应用,尤其是低轨通信卫星“星链”技术的发展,未来对行波管数量的需求,将出现井喷式的发展,开发一种行波管螺旋线的高效检测方法已变得十分迫切。
本文基于双标准棒滚动的螺旋线摆放与调整装置,采用直线取景器和分段阵列编程策略对行波管螺旋线进行了检测,采用激光共聚焦显微镜对行波管螺旋线进行了检测,对比分析了取景器和软件算法的选择对测量误差的影响,得出采用直线取景器和分段阵列编程策略不仅使检测操作效率和灵活性大大提高,而且极大地缩短了检测时间。
2 行波管螺旋线的检测难点
以某波段输出螺旋线为例进行分析,其外形轮廓如
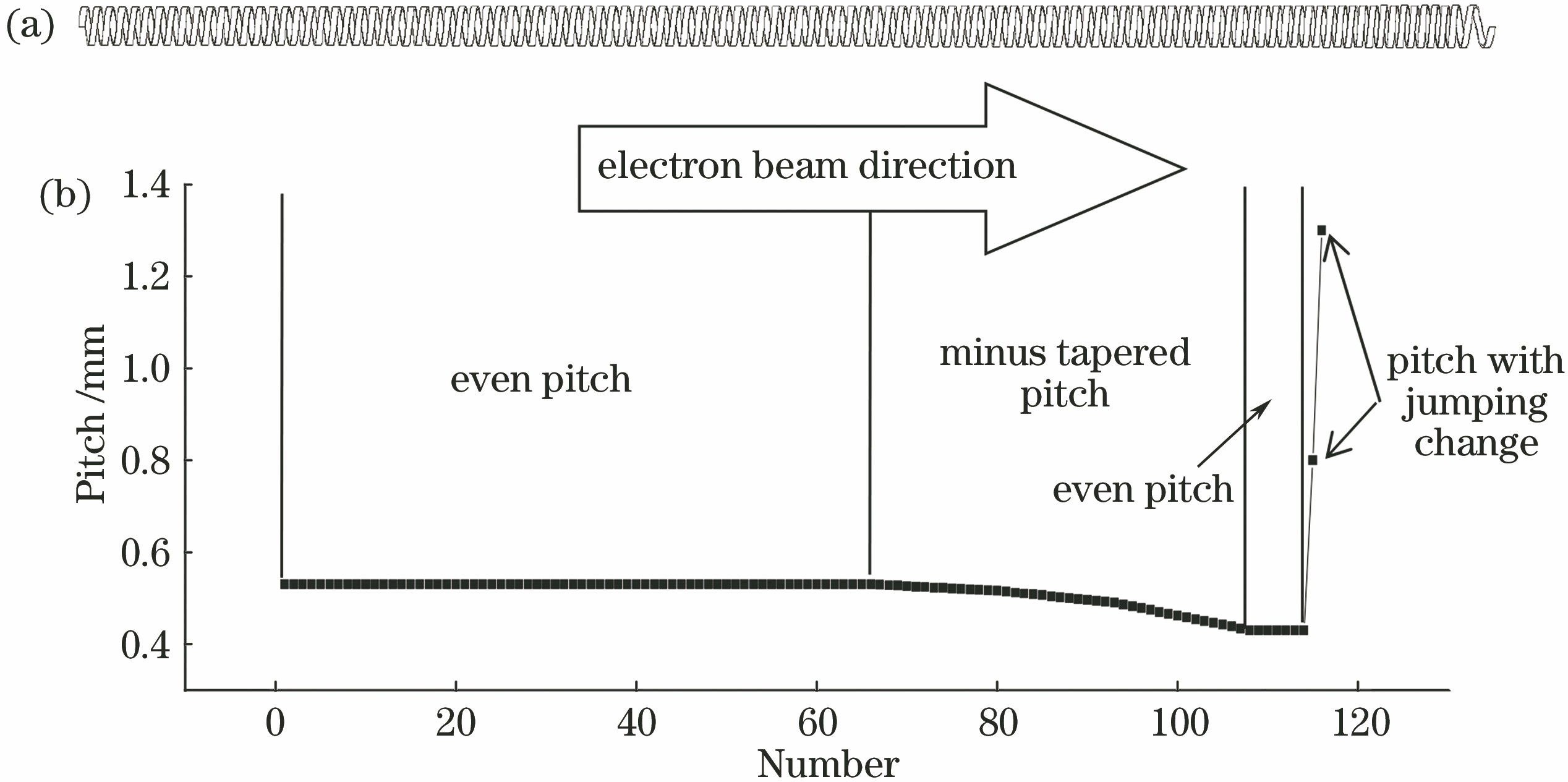
图 1. 行波管螺旋线的基本情况。(a)螺旋线外形;(b)螺距分布
Fig. 1. Basic information of TWT helix. (a) Helix's outline; (b) distribution of pitch
2.1 传统手动测量的难点
传统手工检测的方式如
以上操作过程中,存在的问题有:1)手调压力不稳导致螺旋线变形,2)旋转角度不定导致寻找起始圈效率低,3)手套或指套含有污染物。
2.2 自动测量面对的困难
采用全自动视频影像仪测量时,常见的问题有以下三点:
1) 自动寻边取景器的选择与算法。当选择点测量时:假如摆放直线度、平行度不良,如

图 4. 点测量算法的螺距的测量误差。(a)测量方向与螺旋线轴向不平行;(b)误差来源示意图
Fig. 4. Measurement error of pitch based on point measurement algorithm. (a) Measurement direction deviates from helix axial direction; (b) schematic of error source
点测量取景器无法进行滤波,会导致测量结果产生粗大误差[12]。当选择线测量取景器时,软件只能得出两条线段公垂线的长度,需要将其除以导程角的余弦值换算成螺距,计算过程较为复杂,变螺距的设计带来了导程角的不断变化。
2) 如

图 5. 外径带锥角的螺旋线的摆放高度变化(非比例模型)
Fig. 5. Change of placement height of helix with cone angle in outer diameter (not scaled)
3) 如
2.3 尚存难以检测的项目
绕制后螺旋线内径和外表面粗糙度的检测,靠现有技术手段实现还有以下困难:1)圆柱体零件在测量端面内外径时,可以很方便地竖直摆放在影像仪镜头下,而螺旋线刚度差、长径比大,无法自然直立,采用模具夹紧的操作可能会引起螺旋线的变形;某些低波段螺旋线,如1~2 GHz的L波段,输出螺旋线长度可达280 mm以上,超过了大部分影像仪Z轴的量程(经过调研,大量程的影像仪,一般只扩大XY方向的量程,Z轴恒定为200 mm或250 mm,增加量有限,如需增加Z轴高度,则需要定制或采购特殊的型号);2)螺旋结构的内外表面均无足够面积的平面供探针划测,目前还无法用探针式粗糙度测量仪检测粗糙度,仅能够对绕制之前的展平螺带进行检测。
综合以上分析,行波管螺旋线的检测难点主要集中在:零件摆放,变螺距起始点的寻找,螺距检测软件算法的稳定性,检测效率,内径、粗糙度指标检测技术等。
3 检测方案
3.1 光学测量装置设计
零件摆放与调整的光学测量装置如
针规的直径2Rz,由
式中:Rh为螺旋线的外半径,Rb为圆棒的半径,一般取Rb=(2-2.5)Rh,这是因为选择较粗壮圆棒,可以获得良好的支撑稳定性。
让螺旋线带锥角,可在一端放置一垫片,抬高卡块、两根圆棒,垫片厚度δ的计算公式为
式中:α为螺旋线锥角;L为卡块距离。
采用上述摆放方式时,自动测量过程中镜头高度无变化,仅是从便于测量的方式出发。测量过程中还需计算实测位置与理想位置的差值。二者的余弦误差E为
式中:P'为实测位置的距离;P为真实螺距;n为圈数。
根据计算结果,实测位置与理想位置的差值即余弦误差E可忽略不计。
螺旋线摆放与调整的操作步骤如下:1)在固定条和装置间放一对等直径的大尺寸滚动定位针规,再用活动条压紧上述装置,如
若测量结果显示相邻两个螺距值的偏差方向相反,且都超差,则将一个螺距向公差带方向转动,若另外一个螺距超差更加严重,则可以判定螺旋线起始位置不合格。
滚动定位针规更换的尺寸遵循以下原则:从大到小更换,摆放装置不回退,减小空回误差,螺旋线始终往一个方向转动。
更换过程中,直径差ΔD的计算公式为
式中:β=
如
1: fixture block; 2: plug gauge sleeve; 3: plug gauge; 4: roll plug gauge for location; 5: nut; 6: fixed strip on measuring platform; 7: helix; 8: double-screw bolt; 9: standard round bar; 10: slide-impacted strip on measuring platform; 11: measuring platform

图 7.
螺旋线摆放与调整装置。(a)等轴侧视图;(b)俯视图;(c)剖视图A-A;(d)局部放大视图B;(e)螺旋线被支撑位置与角度
Fig. 7.
Device of placement and adjustment of helix. (a) Isometric view; (b) top view; (c) section view of A-A; (d) partial enlarge view of B; (e) supported position and angle of helix
3.2 建立工件坐标系
以第一圈螺距的起始点为坐标原点进行工件定位,该起始点已由上述零件摆放与调整装置确定。螺旋线自然摆放在两根圆棒内的缝隙上,因此坐标轴向可由圆棒确定。具体的操作办法如

图 8. 在摆放装置上建立工件坐标系。(a)俯视图;(b)左视图
Fig. 8. Workpiece coordinate system on the placement device. (a) Top view; (b) left view
3.3 螺距检测的软件算法分析
螺距的测量程序,主要包含两部分内容:第一部分是前两圈跳变螺距的测量,每次测量完成后,需要人工核对测量值与图纸的误差,并做调整;符合图纸要求后,执行第二部分内容,即完成其他全部螺距的测量。
在软件算法编写上,首先以线取景器在螺带边界构造直线段,设置一定的滤波比例[13],剔除可能出现的毛刺、翻边的影响,如

图 9. 线取景器自动滤波效果图。(a)毛刺示意图;(b)有效滤波;(c)滤波失效
Fig. 9. Automatic filtering effect based on linear viewfinder. (a) Schematic diagram of burr; (b) effective filtering; (c) invalid filtering
表 1. 各策略消耗的时间对比
Table 1. Comparison of time consumed by each strategy
|

图 10. 螺带边界不平行导致的交点距离误差
Fig. 10. Error of distance between intersection points caused by unparallel boundary of helix strip
采用上述自动测量程序,对一根螺旋线进行10次重复测量,得到的结果如
3.4 内外径、锥角的检测
螺旋线的外径,可放置在如
测量端口位置的内径时,依旧将螺旋线摆放在上述V型槽垫块上,侧面增加一套光源、遮光罩、导光管装置,提供一束与螺旋线直径相当的平行光照射螺旋线,采用45°直角棱镜,将轮廓的阴影反射至影像测量仪镜头内,整个内径测量系统如

图 15. 内径自动寻边效果。(a)优化前;(b)优化后
Fig. 15. Automatical search results for the edge of inner diameter. (a) Before optimization; (b) after optimization
为了消除内径测量装置摆放垂直度、光的折反射变形、仪器示值误差带来的影响,可先将与螺旋线设计直径相等的1.4 mm环规和1.6 mm环规放置在V型槽上进行校准,得出测量结果分别为1.4019 mm、1.6022 mm,将之后螺旋线内径的测量结果分别向下修正0.0019 mm和0.0022 mm。
3.5 粗糙度检测
采用OLYMPUS OLS5000激光共聚焦显微镜检测螺旋线外表面粗糙度的照片如

图 16. 螺旋线外表面扫描云图。(a)光学显微镜成像;(b)激光共聚焦显微镜成像
Fig. 16. Scanning cloud chart of helix's outer surface. (a) Optical microscope imaging; (b) laser confocal microscope imaging
为了继续验证测量结果的精度,做了以下两个对比试验:1)分别采用接触式粗糙度轮廓测量仪Hommel T8000SC和上文的激光共聚焦显微镜测量同一根展平的螺带;2)将绕制完成的螺旋线外表面抛光后,复测粗糙度变化。得到了符合工艺规律的结果,如
表 2. 粗糙度测量结果
Table 2. Roughness measurement results
|
1) 对同一根螺带的测量,激光共聚焦显微镜与传统接触式设备的差值为
2) 螺带经绕制后,表面粗糙度略有下降,下降量为
3) 表面经磨削后,粗糙度得到了明显改善,改善量为
4 结论
从行波管螺旋线的工程应用角度考虑,开发了两种检测装置,提高了零件摆放与调整的效率、精度和洁净度;具体测量时,举例说明取景器和软件算法的选择对测量误差的影响,最终采用直线取景器和分段阵列编程策略对行波管螺旋线进行了检测;选择激光共聚焦显微镜检测粗糙度:以上共同构成了一套相对完整的行波管螺旋线检测方案。具体指标如下:
1) 基于双标准棒滚动的螺旋线装置,使零件的摆放直线度优于0.01 mm,旋转角度可按目标值步进,仅调整1~2次就能找到变螺距的起始位置,调整过程不存在应力集中、手套污染等问题。
2) 测量软件的直线取景器对螺带的自动寻边过程稳定,将直线与螺旋线轴线或轴线平行线的交点作为螺距特征点,具有较好的算法稳定性,测量结果重复性优于0.8 μm。
3) 采用分段阵列的编程策略,检测变螺距螺旋线,具有较高的操作效率和灵活性,一根116圈的螺旋线,总检测时间约为传统方式的三分之一,同时测量多根时,效率提升效果将更加明显。
4) 基于45°直角棱镜开发了端口处内径测量系统,使螺旋线水平放置在V型槽上即可完成检测,获得了对比度鲜明的成像效果。
5) 基于激光共聚焦显微镜测量了螺旋线外表面粗糙度,得到了与工艺规律相吻合的数据,测量结果与传统接触式设备的差值为2.6%。
[1] Gilmour AS, Jr. Klystrons, traveling wave tubes, magnetrons, crossed-field amplifiers, and gyrotrons[M]. Boston: Artech House, 2011.
[2] 冯程. 基于周期金属圆柱的微带曲折线行波管研究[D]. 南京: 东南大学, 2018: 3- 12.
FengC. Research on microstrip meander line traveling wave tube based on periodical metallic rods[D]. Nanjing: Southeast University, 2018: 3- 12.
[3] Ghosh T K, Challis A J, Jacob A, et al. Design of helix pitch profile for broadband traveling-wave tubes[J]. IEEE Transactions on Electron Devices, 2009, 56(5): 1135-1140.
[4] D'Agostino S. Paoloni C. Cathode voltage adjustment to compensate helix pitch tolerance in TWTs[J]. Electronics Letters, 2004, 40(1): 36-38.
[5] Zhang XM, YangG, Ou HL, et al. Theoretical investigation into an ultra-wideband helix traveling-wave tube[C]∥2019 International Vacuum Electronics Conference (IVEC), April 28-May 1, 2019, Busan, Korea (South). IEEE, 2019: 18792381.
[6] Ghosh TK, JacobA, TokeleyA, et al. Optimization of helix pitch profile for broadband Mini-TWTs[C]∥2008 IEEE International Vacuum Electronics Conference, April 22-24, 2008, Monterey, CA, USA. IEEE, 2008: 10072808.
[8] 王小宁, 苏小保, 肖刘. 高效率双频段Ka/Q毫米波行波管螺旋慢波系统的研究[J]. 真空科学与技术学报, 2016, 36(11): 1234-1240.
Wang X N, Su X B, Xiao L. Design ofhigh-efficiency Ka/Q dual-band millimeter-wave helix traveling wave tube slow wave structure[J]. Chinese Journal of Vacuum Science and Technology, 2016, 36(11): 1234-1240.
[9] 唐康淞, 赵刚, 李实, 等. 双渐变螺旋线慢波结构参数分析及优化[J]. 强激光与粒子束, 2008, 20(9): 1507-1510.
Tang K S, Zhao G, Li S, et al. Analysis and optimization of parameters of double-taper helical slow-wave structure[J]. High Power Laser and Particle Beams, 2008, 20(9): 1507-1510.
[10] 李鑫伟, 王小宁, 俞世吉, 等. 星载螺旋线行波管螺旋线过盈装配技术研究[J]. 真空科学与技术学报, 2016, 36(9): 1017-1023.
Li X W, Wang X N, Yu S J, et al. Simulation of interference-fit of helix in assembling space helix traveling wave tube[J]. Chinese Journal of Vacuum Science and Technology, 2016, 36(9): 1017-1023.
[11] 陈聪. 行波管结构设计及加工误差分析[D]. 成都: 电子科技大学, 2016: 35- 46.
ChenC. Traveling wave tube structure design and the error analysis of the processing[D]. Chengdu: University of Electronic Science and Technology of China, 2016: 35- 46.
[12] 徐新华, 王青, 钱峥, 等. 基于图像处理的铟钢尺自动检测系统[J]. 光学学报, 2009, 29(6): 1519-1522.
[13] 郭海涛, 田坦, 王连玉, 等. 利用二维属性直方图的最大熵的图像分割方法[J]. 光学学报, 2006, 26(4): 506-509.
[14] 肖青, 王兴龙, 傅谦, 等. 一种用于厚度在线检测的光学装置[J]. 光学学报, 2015, 35(2): 0223002.
[15] 刘中生, 彭履忠, 李艳, 等. 大尺寸外圆锥锥角偏差及素线直线度误差的测量[J].计量学报, 1991( 4): 257- 261, 274.
Liu ZS, Peng LZ, LiY, et al. Measurement of taper angle deviation and generatrix straightness of machined parts with large sizes[J]. Acta Metrologica Sinica, 1991( 4): 257- 261, 274.
[16] 吴晓军, 郭亚雪. 一种圆柱物体360°全景成像装置设计方法[J]. 光学学报, 2015, 35(9): 0923002.
[17] 中华人民共和国国家质量监督检验检疫总局, 中国国家标准化管理委员会. 产品几何技术规范(GPS) 表面结构轮廓法表面粗糙度参数及其数值: GB/T 1031—2009[S]. 北京: 中国标准出版社, 2009.
General Administration of Quality Supervision, InspectionandQuarantine of the People's Republic of China & Standardization Administration of the People's Republic of China. Geometrical product specifications (GPS)-surface texture: profile method-surface roughness parameters and their values: GB/T 1031—2009[S]. Beijing: Standards Press of China, 2009.
[18] 陈海平, 李佳斌, 刘长春, 等. 基于角差法面形测量装置的测角误差研究[J]. 光学学报, 2014, 34(10): 1012003.
[19] 崔天刚, 张宏吉, 马文生, 等. Wolter I型反射镜面形检测装置的改进[J]. 光学学报, 2011, 31(4): 0412007.
[20] International Organization forStandardization. Geometrical product specifications (GPS). Surface texture: Areal-Part 2: terms, definitions and surface texture parameters: ISO 25178-2:2012[S]. Switzerland: IHS, 2012.
Article Outline
王建, 李飞, 方有维. 行波管螺旋线的光学检测方法[J]. 光学学报, 2020, 40(9): 0912001. Jian Wang, Fei Li, Youwei Fang. Optical Measurement Method for a Traveling Wave Tube Helix[J]. Acta Optica Sinica, 2020, 40(9): 0912001.