液相下激光烧蚀快速制备图案化铜微纳结构
下载: 619次
1 引 言
金属具有良好的延展性、导电性、导热性和抗摩擦性等特性,广泛应用于生产生活中,如半导体器件、基础设施和工业设备等[1]。金属表面微纳结构化产生诸多优于体材料的特性并展现出新的性能,如浸润性[2]、热辐射[3]、耐腐蚀[4]和结构色[5]等,因此成为科学界和工业界关注的热点,是当前金属表面技术中重要的研究方向。
过去的二十年里,金属表面微纳结构制造技术得到了大量的研究,如光刻[6-7]、电化学[8-9]
在众多金属材料中,铜金属不仅在自然界中储量丰富,而且还具有高导电性、热稳定性和优良的催化活性等性能。本文采用激光烧蚀技术在液相下快速制备了大面积图案化铜微纳结构,研究了激光功率、扫描速度和扫描次数等参数对铜微纳结构的影响,分析了激光加工过程中微纳结构的形成机制。此外,还研究了图案化铜微纳结构对纯净水和食用油的浸润性。
2 实 验
2.1 Cu2O微米粒子制备实验
本实验采用水热还原法制备氧化亚铜微米颗粒(Cu2O microparticles,Cu2O-MPs)。首先,在磁力搅拌下,将0.88 g硝酸铜和1.36 g聚乙烯吡咯烷酮分别加入30 mL和60 mL乙二醇溶液中。搅拌至完全溶解(约30 min)后,将上述溶液充分混合并转入聚四氟乙烯内衬的不锈钢高压反应釜中,在160 ℃下加热6 h。最后,通过离心清洗(7 000 r/min)获得Cu2O-MPs,室温下分散在乙醇溶液中备用。
2.2 激光烧蚀制备图案化铜微纳结构实验
本实验以Prime级单晶硅(尺寸为1 cm×1 cm,厚度为50 μm,晶面为(100)晶面,单面抛光)作为衬底材料,采用光纤激光加工系统(型号为FB20-1,长春新产业光电技术有限公司)在液相条件下制备图案化铜微纳结构。该激光器波长为1 064 nm,脉宽约为100 ns,激光光斑直径约为50 μm,频率为20 kHz。
图1为激光烧蚀制备图案化铜微纳结构的示意图。首先,使用超声波依次在丙酮、乙醇和去离子水中清洗硅衬底,以去除表面有机物和其他杂质。随后,将清洗后的硅衬底放置在加工池中,并注入含有Cu2O-MPs的乙醇分散液。设置不同组合激光参数的纳秒激光进行加工,从而制备图案化铜微纳结构。本实验中,在50 μm的结构周期下,研究激光功率(1,2,3,4和5 W)、扫描速度(125,100,75,50和25 mm/s)和扫描次数(1~10)等参数对图案化铜微纳结构的影响。

图 1. 激光烧蚀制备图案化铜微纳结构示意图
Fig. 1. Schematic diagram of patterned Cu micro-nano structure prepared by laser ablation
2.3 测量与表征
通过扫描电子显微镜(SEM,FEI Quanta 250)对图案化铜微纳结构的形貌进行表征和分析。利用能量色散X射线光谱仪(EDS,Aztec 3.3)和X射线衍射仪(XRD,Y-2000)分析图案化铜微纳结构的元素组成和晶体结构,采用共聚焦显微镜(CSM 700)研究图案化铜微纳结构的平均粗糙度。使用接触角测量仪(DSA100)测定了样品对水和食用油的浸润性(水为娃哈哈纯净水,食用油为金龙鱼玉米胚芽油)。
3 结果与讨论
3.1 图案化铜微纳结构的形貌结构表征
图2(a)~2(e)显示了在相同扫描速度(100 mm/s)和扫描次数(4次)时,不同激光功率(分别为1~5 W)下铜微纳结构的SEM图像和局部放大图。如图2(a)所示,激光功率为1 W时,由于激光光斑中心区域的能量和温度大于光斑边缘位置,中心区域的铜颗粒部分气化,从而形成纳米级铜颗粒[22,24]。从图2(a)的光斑边缘放大图可以观察到,铜颗粒仅有轻微烧蚀痕迹,这是因为高斯光斑边缘位置激光能量较低[25]。对SEM图进行快速傅里叶变换(Fast Fourier Transform, FFT)后生成频谱图(插图),从明暗频率分布可以看出图案化铜微纳结构为周期性结构。当结构分布存在多个对称轴时,在FFT频谱图中则存在多对中心对称的频率分量。通过选取第一级频率分量(距离中心零频率分量最近的一对呈中心对称的频率分量),根据其频率分布进行计算,可以得到制备的图案化铜微纳结构周期约为52.3 μm。制备结构周期与设计值相差2.3 μm。当激光功率升至2 W时,如图2(b)所示,光斑中心区域依然只有少量的铜纳米颗粒,但是光斑边缘位置形成的微米级颗粒明显增多,并且微米级颗粒分布在光斑交界处形成微岛结构。图2(b)的光斑边缘放大图还显示出此条件下颗粒的熔融程度加剧,颗粒之间的聚集现象更加明显。由频谱图可以看出,结构轮廓边缘越清晰,频谱图中明暗对比越强烈,与结构的周期性存在明显的对应关系。根据频率分布计算得出制备的结构周期约为51.2 μm,与设计值的误差减小至1.2 μm。激光功率增加至3 W时,如图2(c)所示,由于激光能量的增加,光斑中心位置形成的纳米颗粒粒径明显增加,光斑交界处的微米级颗粒进一步熔融聚集。FFT频谱图中显示,明暗对比减弱,对应于图2(c)中有序度降低的现象。经计算,结构周期约为51.6 μm,误差为1.6 μm。随着激光功率继续增加到4 W和5 W时,铜微纳结构发生了明显的变化。如图2(d)和2(e)所示,硅片表面大部分激光扫描区域发生熔融现象,结构轮廓边缘的清晰度明显下降。光斑中心位置因高激光功率作用会产生飞溅物,这些飞溅物与熔融金属颗粒混合后会迅速冷却并凝固在光斑交界处[13]。根据FFT的频谱图计算得到结构周期分别约为52.5 μm和52.4 μm,与设计值的误差进一步增大。以上结果表明,随着激光功率的增加,结构的周期与设计值的误差呈现先减小后增加的趋势,在激光功率为2 W时,误差最小。此外,在激光加工过程中,样品表面会发生熔融现象,且该现象随激光功率的增加而加剧。当激光能量适宜时,在光斑中心高能量区域形成纳米颗粒,而边缘低能量区域金属颗粒因熔融而聚集成微岛结构,由此形成图案化铜微纳结构。
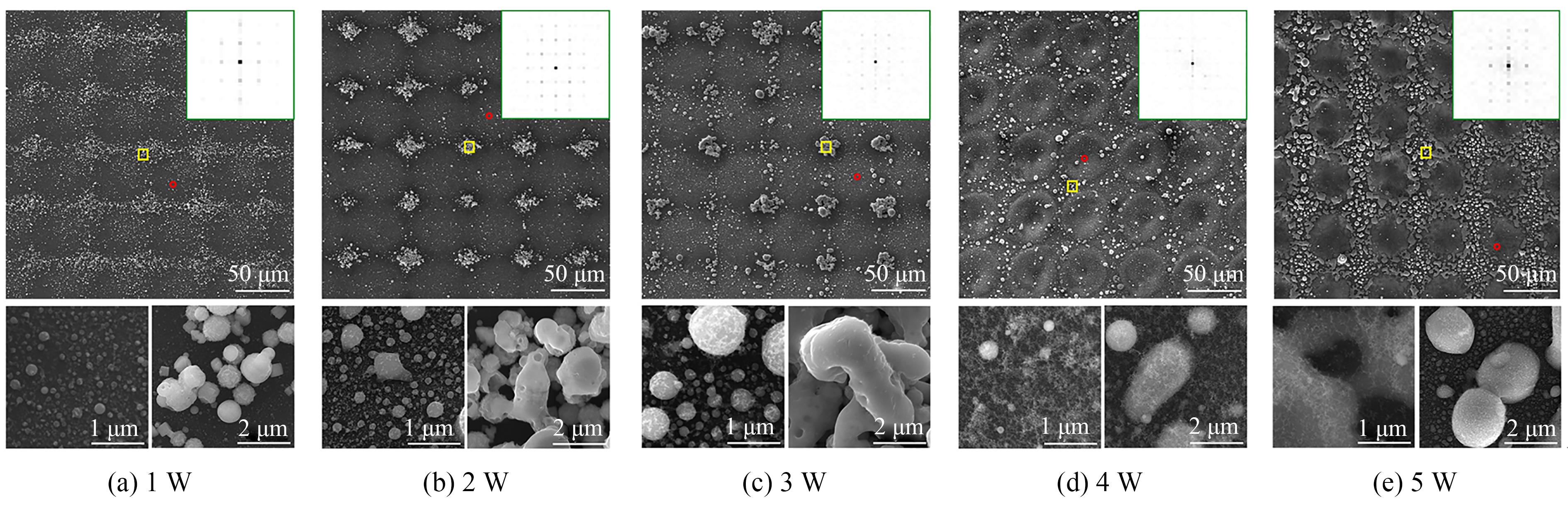
图 2. 扫描速度为100 mm/s时不同激光功率下制备的铜微纳结构SEM图像(插图为傅里叶变换后频谱图)
Fig. 2. SEM images of Cu micro-nano structure prepared at scanning speed of 100 mm/s with different laser powers(Illustration is Fast Fourier Transform spectrum)
除激光功率外,扫描速度也是影响铜微纳结构的关键因素之一。图3(a)~3(e)展示了扫描4次,激光功率为2 W时,不同扫描速度(125,100,75,50和25 mm/s)对铜微纳结构形成的影响。当扫描速度较快(见图3(a)和3(b))时,激光烧蚀在同一点持续的时间较短,光斑交界位置形成的微米级铜颗粒的熔融程度较轻,颗粒之间的聚集程度较低。通过FFT频谱图计算得到结构周期分别约为52.8 μm和51.2 μm,导致误差明显不同的主要原因是铜颗粒的尺寸差异。当扫描速度降低至75 mm/s和50 mm/s时,每个烧蚀位置都受到连续脉冲的影响且随着Cu2O-MPs分散液的不断补充,在光斑边缘位置聚集了更多的熔融铜微纳颗粒。这些熔融铜微结构在液相下快速冷却和凝固,在光斑交界处形成新的微点阵结构,如图3(c)和3(d)所示。从光斑边缘放大图可以发现,形成的微岛结构的致密性也有所增加。与此同时,在光斑中心区域形成了更多的纳米颗粒。FFT频谱图显示,当扫描速度为50 mm/s时,中心对称的多级频率分量明暗对比更加强烈,结构的周期性较好,计算得到的周期约为50.9 μm,与设计值更加接近。随着扫描速度的继续降低(见图3(e)),激光在同一点烧蚀时间过长[26],会使熔融聚集的金属颗粒再次发生熔融现象,颗粒的粒径明显增大,由FFT频谱计算周期约为55.6 μm,与设计值的误差较大。
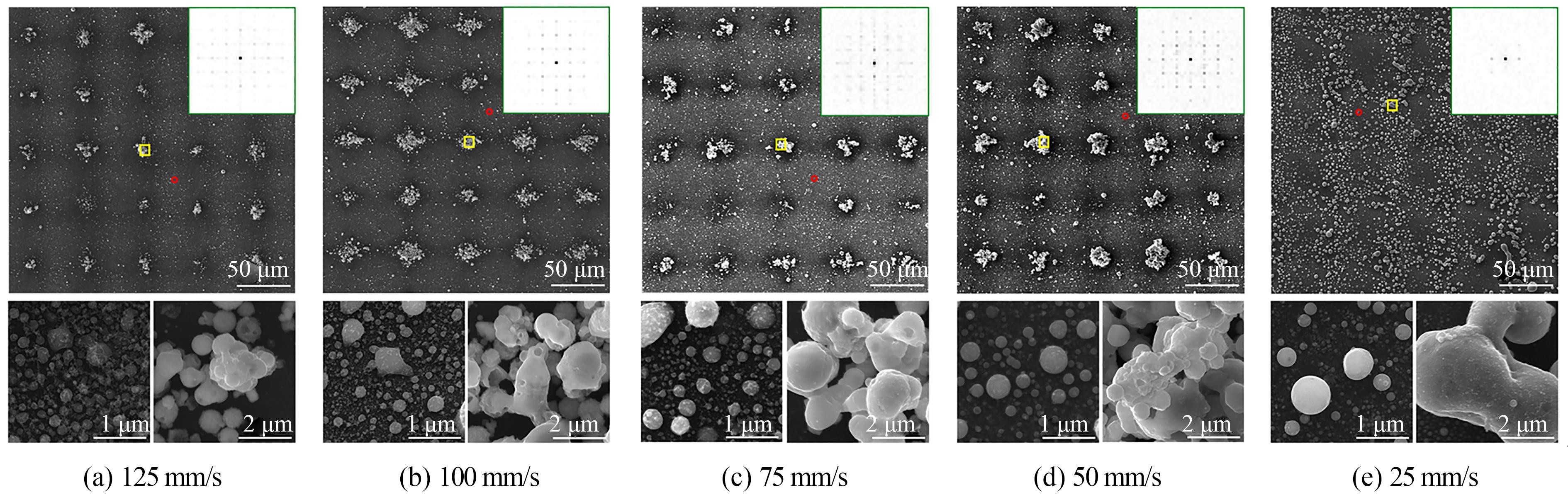
图 3. 激光功率为2 W时不同扫描速度下制备的铜微纳结构SEM图像(插图为傅里叶变换后频谱图)
Fig. 3. SEM images of Cu micro-nano structure prepared at laser power of 2 W with different scanning speeds (Illustration is a Fast Fourier Transform spectrum)
扫描次数也是影响样品表面形貌结构的重要因素之一[27]。图4(a)~4(j)为相同扫描速度(50 mm/s)和激光功率(2 W)时,不同扫描次数(1~10次)下形成的图案化铜微纳结构的SEM图像和FFT频谱(插图)。如图4(a)所示,当扫描次数仅为1次时,光斑交界处的非辐照区域形成的微米颗粒分布较为分散,且光斑中心处形成的纳米颗粒较小,对约1 000个纳米颗粒的粒径进行统计,如表1所示,97.3%以上的纳米颗粒小于200 nm。经过FFT频谱计算制备微纳结构的周期约为54.4 μm,与设计值相差4.4 μm。当扫描次数增加时(见图4(b)和4(c)),光斑中心和边缘位置形成的颗粒数量均明显增加,中心区域小于200 nm的纳米颗粒比例逐渐减少,较大尺寸的纳米颗粒比例逐渐增多。另外,位于光斑边缘处的颗粒存在熔融再聚集成更大金属颗粒的趋势。制备的结构周期与设计值误差从3.3 μm减小到1.7 μm。如图4(d)~4(h)所示,当扫描次数进一步增加时,微岛结构更加规律地分布在光斑之间未辐照的区域,而光斑中心位置亚微米级的纳米颗粒的比例随之增大。当扫描次数达到5次以上时,中心位置粒径大于500 nm的颗粒数量明显增加。通过FFT频谱计算得到图案化铜微纳结构的周期分别约为50.9,50.7,50.3,50.5和51.0 μm,制备的结构与设计值误差呈现先减小后增大的趋势。当扫描次数为6次时,频谱中存在较多中心对称的多级频率分量对,且明暗对比较强烈,制备的结构周期与设计值的误差最小。当扫描次数增长至9次和10次时(见图4(i)和4(j)),颗粒的熔融现象更加明显,光斑中心位置颗粒的尺寸明显增大且无序度增加。制备的微纳结构周期误差也随之增大,由1.5 μm增至2.1 μm。产生上述现象的原因如下:随着扫描次数的增加,光斑中心位置会吸收更多的激光能量[28],产生大量的熔融纳米颗粒,这些纳米颗粒之间相互融合从而在中心位置形成尺寸更大的颗粒。此外,在激光照射区域会产生一定的等离子体,这些等离子体向两侧飞溅,聚集在激光非辐照区域并冷却沉积,从而形成复合的微纳混合结构。
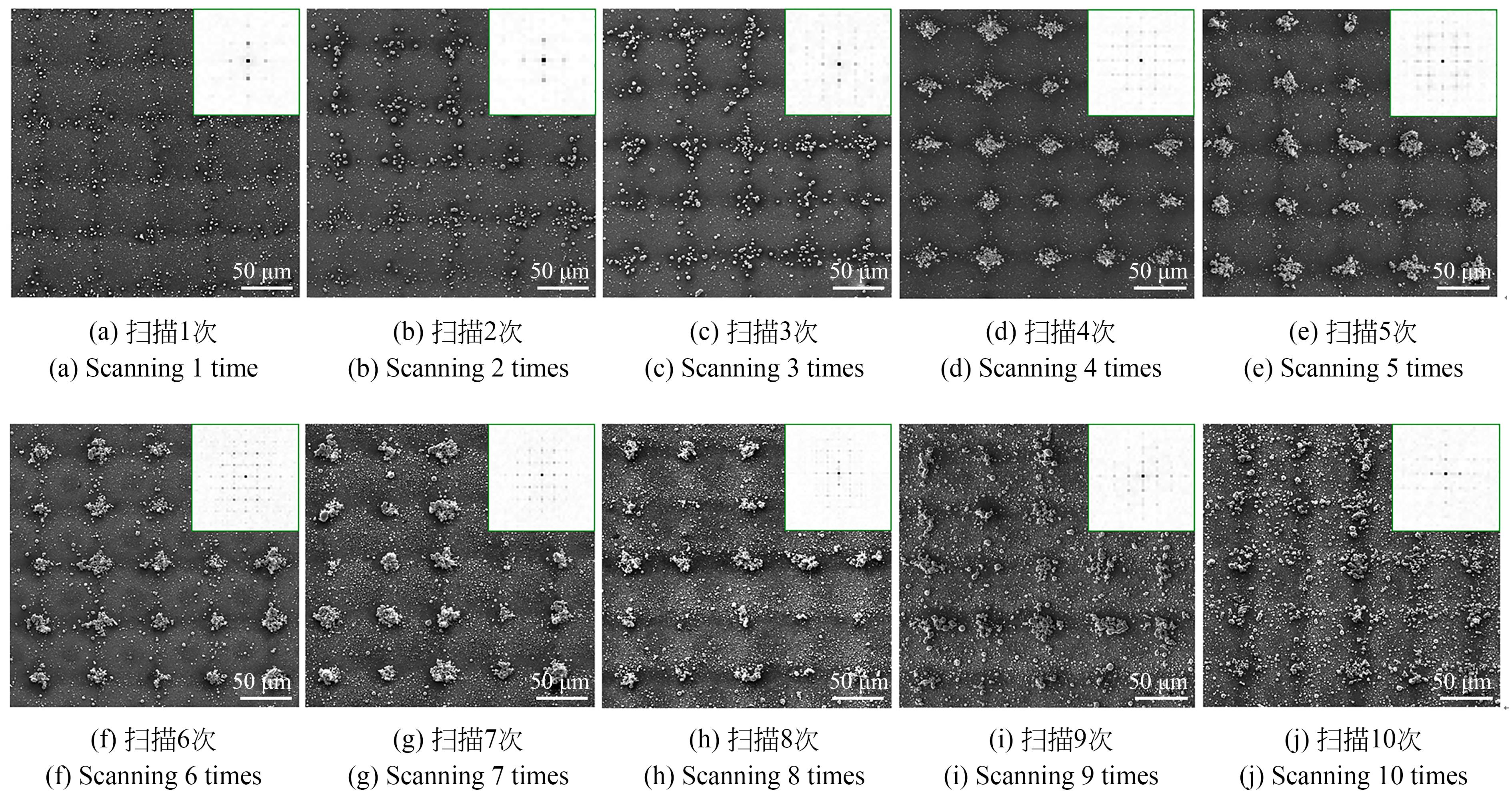
图 4. 激光功率为2 W,扫描速度为50 mm/s时不同扫描次数下制备的铜微纳结构SEM图像(插图为傅里叶变换后频谱)
Fig. 4. SEM images of Cu micro-nano structure prepared with different scanning times at laser power of 2 W and scanning speed of 50 mm/s(illustration is Fast Fourier Transform spectrum)
表 1. 扫描次数对光斑中心颗粒粒径的影响
Table 1. Effect of scanning times on particle size in center of laser spot
|
3.2 EDS和XRD分析
为了确定图案化铜微纳结构的元素组成,采用EDS进行表征。图5(a)为图案化铜微纳结构的EDS能谱,经过分析可知该结构含有Cu,Si,O和C元素。然后,随机选取一个区域对图案化铜微纳结构进行元素面扫描测试。相应的元素映射图像如图5(b)~5(f))所示,Cu元素分布在整个样品表面,含量大约为17.69%,主要对应于图5(c)中较亮的区域。其中,光斑中心区域Cu元素信号较弱,光斑交界微点阵处Cu元素信号更强,这是由于光斑中心区域Cu含量较少,而光斑交界处Cu含量较高。此外,EDS结果显示Si元素信号最强,占比约为65.27%,其原因是衬底为硅片。从图5(e)中观察到Si元素含量几乎不会分布在微点阵区域,进一步证明此处存在更多的铜金属颗粒。O元素(见图5(f))含量最少,可能源自硅基底表面的氧化膜和Cu2O-MPs中含有的O。以上分析表明,液相激光烧蚀技术成功地在硅片表面沉积了铜金属,并且形成微纳复合结构。
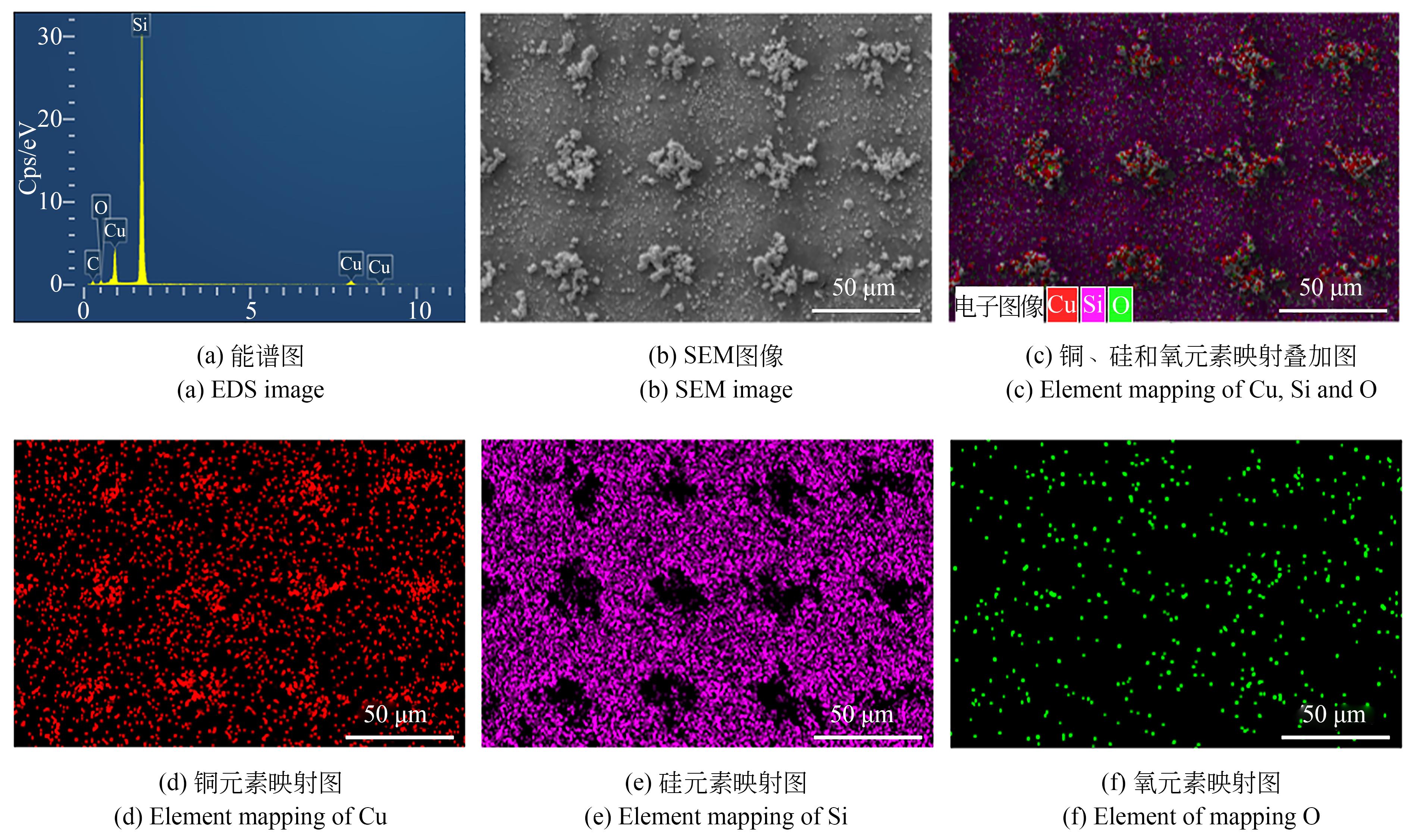
图 5. 扫描4次的铜微纳结构的EDS能谱及元素映射图
Fig. 5. EDS and element mapping images of Cu micro-nano structure prepared by scanning 4 times
对图案化铜微纳结构进行了XRD测试,如图6所示,位于36.4°,61.3°和69.3°处的衍射峰分别与Cu2O的(111)和(220)晶面相对应;位于43.3°和74.1°处的衍射峰与铜的(111)和(220)晶面相对应,由此证明Cu2O和Cu同时存在于图案化铜微纳结构中,说明部分Cu2O颗粒经激光诱导还原生成Cu。
3.3 激光烧蚀演变过程分析
基于激光加工参数对微纳结构的影响规律,分析了溶液中纳秒激光烧蚀形成图案化铜微纳结构的机理。通过比较不同激光参数下图案化铜微纳结构的形貌差异,并进行EDS和XRD分析,初步推断微纳结构是由激光诱导金属熔融再凝固积累而形成的[13]。纳秒激光加工金属的主要作用是热效应,由于纳秒激光具有较大的峰值功率,材料表面发生熔融。在激光加工过程中,Cu2O-MPs中的电子吸收大量光子[29]。随后,电子在短时间内转移到晶格中,引起热扩散,使金属颗粒的温度迅速升高,导致金属颗粒的熔化和蒸发,从固态转变为液态或气态,甚至形成等离子体。由于辐射区域和附近未辐射区域之间存在明显的温差,从而产生马兰戈尼效应,这一效应驱使熔融金属向激光照射位置边缘移动。
当扫描次数为1次时,单位面积接收的激光能量较少,因此只有少量铜颗粒聚集在硅片表面,其周期性分布不明显,如图7(a)所示。然而,随着扫描次数增加到4次,单位面积接收的激光能量增加,可以观察到光斑边缘位置聚集的铜颗粒增多,如图7(b)所示。此外,EDS分析也证实这些位置Cu元素相对含量较多(见图5(d)),且周期性分布更加明显。随着扫描次数的进一步增加和Cu2O-MPs分散液的补充,熔融金属不断聚集形成微岛状结构,如图7(c)所示。在激光加工过程中,激光诱导等离子体形成的纳米团簇会不断地沉积到已加工区域和微岛结构表面[30-31]。通过图7(c)中的SEM插图可以观察到微岛结构表面随机分布大量纳米颗粒。
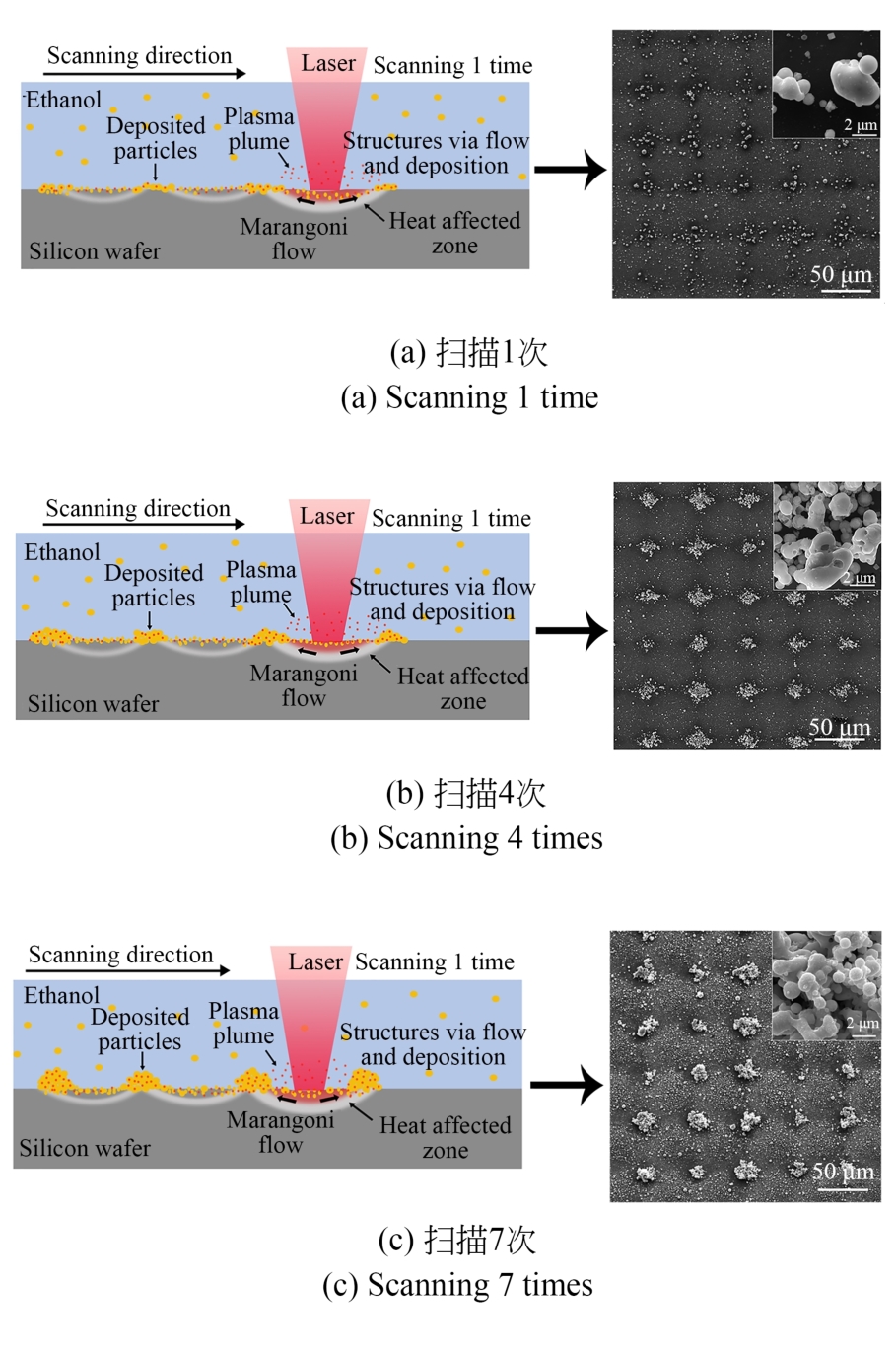
图 7. 液相下激光烧蚀图案化铜微纳结构的演变过程
Fig. 7. Evolution of patterned Cu micro-nano structure by laser ablation in liquid
由实验结果可知,在激光加工过程中,图案化铜微纳结构的形貌特征与扫描次数是有一定相关性和规律性的,即当扫描次数增加时,光斑交界处的非烧蚀区域聚集的铜颗粒增多,形成微岛结构,并且微岛结构表面分布着大量纳米颗粒。
3.4 浸润特性
由于激光加工参数不同,硅片表面形成不同的图案化铜微纳结构,相应地,表面粗糙度也不尽相同。表2为不同扫描次数下样品表面的平均粗糙度统计结果。随着扫描次数从1增长至7后,样品的表面粗糙度呈现增加趋势。而当扫描次数达到7次以上时,粗糙度开始减小。样品表面粗糙度是影响其浸润特性的关键因素之一,因此,随后针对样品表面粗糙度开展浸润特性的研究。
表 2. 扫描次数对图案化铜微纳结构表面粗糙度的影响
Table 2. Effect of roughness of patterned Cu micro-nano structure on different scanning times
|
一般来说,静态接触角(Contact Angle, CA)大于150°的表面被定义为超疏水表面。在自然界中,荷叶具有明显的超疏水自清洁性能,人们称这种自清洁过程为“荷叶效应”[32]。随后,人们也在玫瑰花瓣上发现了类似的效应,称为“花瓣效应”[33]。不同之处在于该表面除了超疏水性能外,还对水有很强的附着力,即使将花瓣倒置,水滴也不会滚落[33]。由此可见,“花瓣效应”与“荷叶效应”相似,但仍有区别。超疏水有两种可能的模型:(1)一部分液体完全浸入固体表面结构(Wenzel model)[34];(2)液体与固体表面结构之间留有空气(Cassie-Baxter model)[35]。Wenzel model 可以用以下方程来描述浸润性:
式中:θw和θy分别为Wenzel接触角和Young接触角,r为粗糙度因子,表示粗糙表面的实际面积与其投影面积之比。
Cassie-Baxter模型用来描述非均质浸润,即:
式中:θc和θy分别为Cassie-Baxter接触角和Young接触角,r为固体表面被液体浸润的实际面积与投影面积之比,f为投影浸润面积的面积分数。
在Cassie-Baxter体系中,液体只停留在凸出结构的表面,故此液滴下表面会与微观结构构建相对稳定的空间,形成所谓的“气穴”。另一方面,针对“花瓣效应”,基于Cassie模型发展的Cassie-impregnating模型[36]进行解释更为合理,Cassie-impregnating模型认为液滴完全渗透到微米结构之间,但只能部分渗透到纳米结构之间。因此,Cassie-impregnating被认为是一种中间状态,液体浸润表面的比例低于Wenzel状态,但却高于Cassie-Baxter状态。
图8为低黏附(Cassie-Baxter状态)和高黏附(Cassie-impregnating状态)超疏水表面液滴示意图。在Cassie-Baxter体系中,由于液滴仅停留在纳米结构顶端,在微观结构之间部分下垂形成气穴,因此液滴具有非常低的接触角迟滞(CAH)和黏附力。针对Cassie-impregnating状态,存在于纳米结构间隙的气穴使得微观结构完全渗透和纳米结构部分渗透,导致该结构存在高CA和高CAH状态[37]。
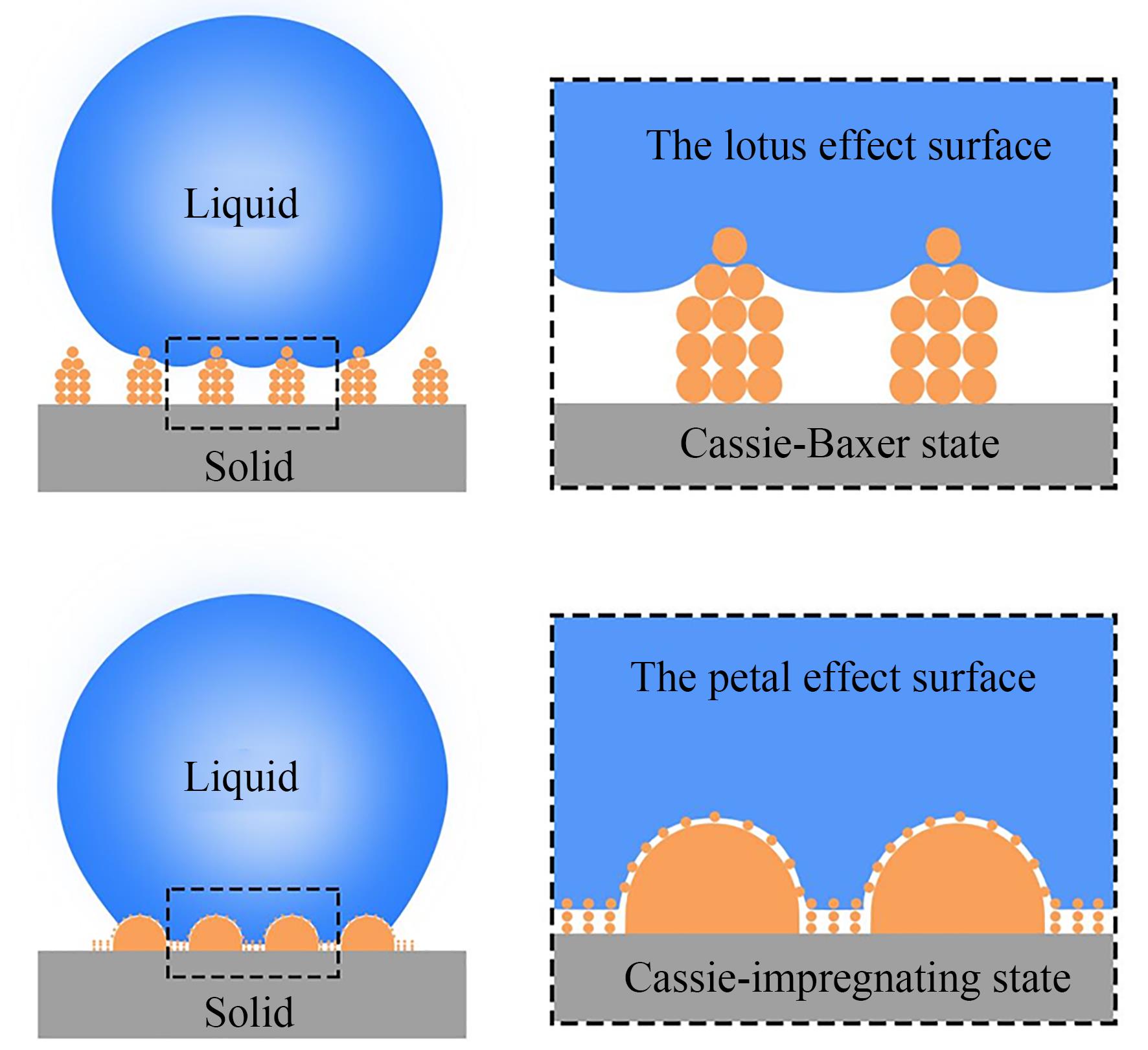
图 8. 低黏附(Cassie-Baxter状态)和高黏附(Cassie-impregnating状态)超疏水表面液滴示意图
Fig. 8. Schematic of droplets on superhydrophobic surfaces with low adhesion (Cassie-Baxter state) and high adhesion (Cassie-impregnating state)
本文分别测量了不同扫描次数下制备样品的食用油和纯净水接触角,以研究图案化铜微纳结构的疏油疏水能力。图9显示了不同样品的油接触角,整体呈现高斯分布。当扫描次数为1和2时,结构表面表现出显著的亲油性。随着扫描次数增加至6和7时,样品表面的油接触角逐渐增大,分别达到(100.0±1.3)°和(101.0±2.0)°,呈现疏油性。当扫描次数为8及以上时,油接触角开始减小。可见,样品对油的浸润性能与粗糙度变化规律有密切的关系,均呈现先增加后缓慢下降的趋势。
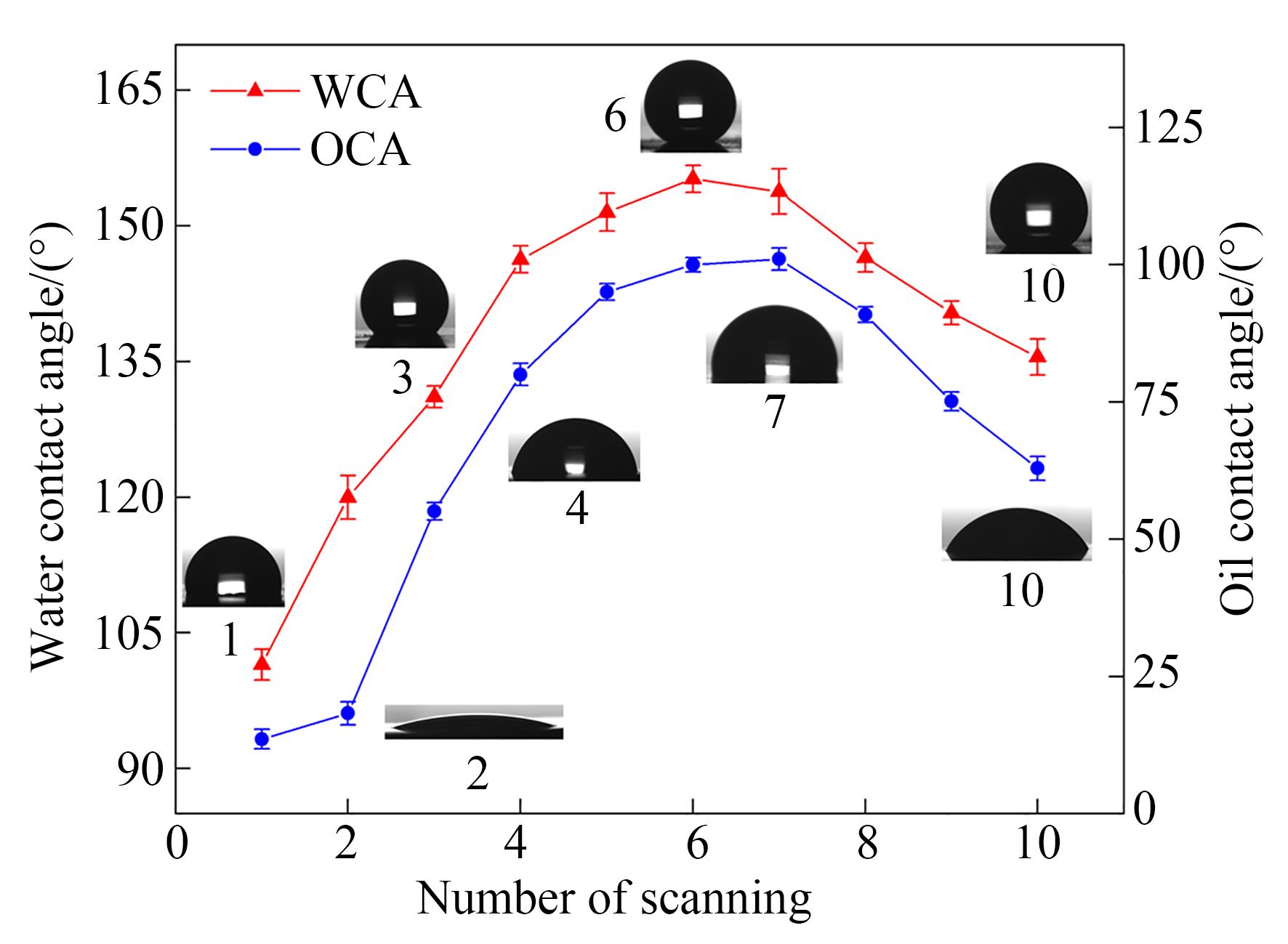
图 9. 不同扫描次数下制备的图案化铜微纳结构的水接触角和油接触角
Fig. 9. Water contact angle and oil contact angle of patterned Cu micro-nano structure with different scanning times
从图9可以看出,样品对水的浸润性与食用油的浸润性变化趋势相似,扫描1~10次后,接触角变化亦呈现高斯分布。扫描1~3次后,水接触角之间的差值变化较大,达到29.6°;而扫描4~6次后,疏水角变化趋于平缓,差值为7.1°。当扫描次数为6时,图案化铜微纳结构水接触角达到(155.2±1.5)°,表现出超疏水性,优于同类铜基材料[38-42],且明显高于硅片表面水接触角[43]。当扫描次数为7~10后,接触角开始下降,并呈现线性递减的趋势。这与样品表面粗糙度的变化趋势一致。
由许多独立的微岛和纳米颗粒组成的图案化铜微纳结构表面具有“花瓣效应”,且每个微岛表面均覆盖少量纳米颗粒构成微纳跨尺度的二元结构[36]。显然这些二元结构对表面粗糙度具有重要贡献。当样品表面垂直或上下翻转时,微结构之间形成的气穴就会产生负压,对水滴产生吸引力,从而贡献为水滴与表面的黏附力,如图10所示。即使当样品垂直或倒置时,水滴依然保持近球形状态或球形状态。
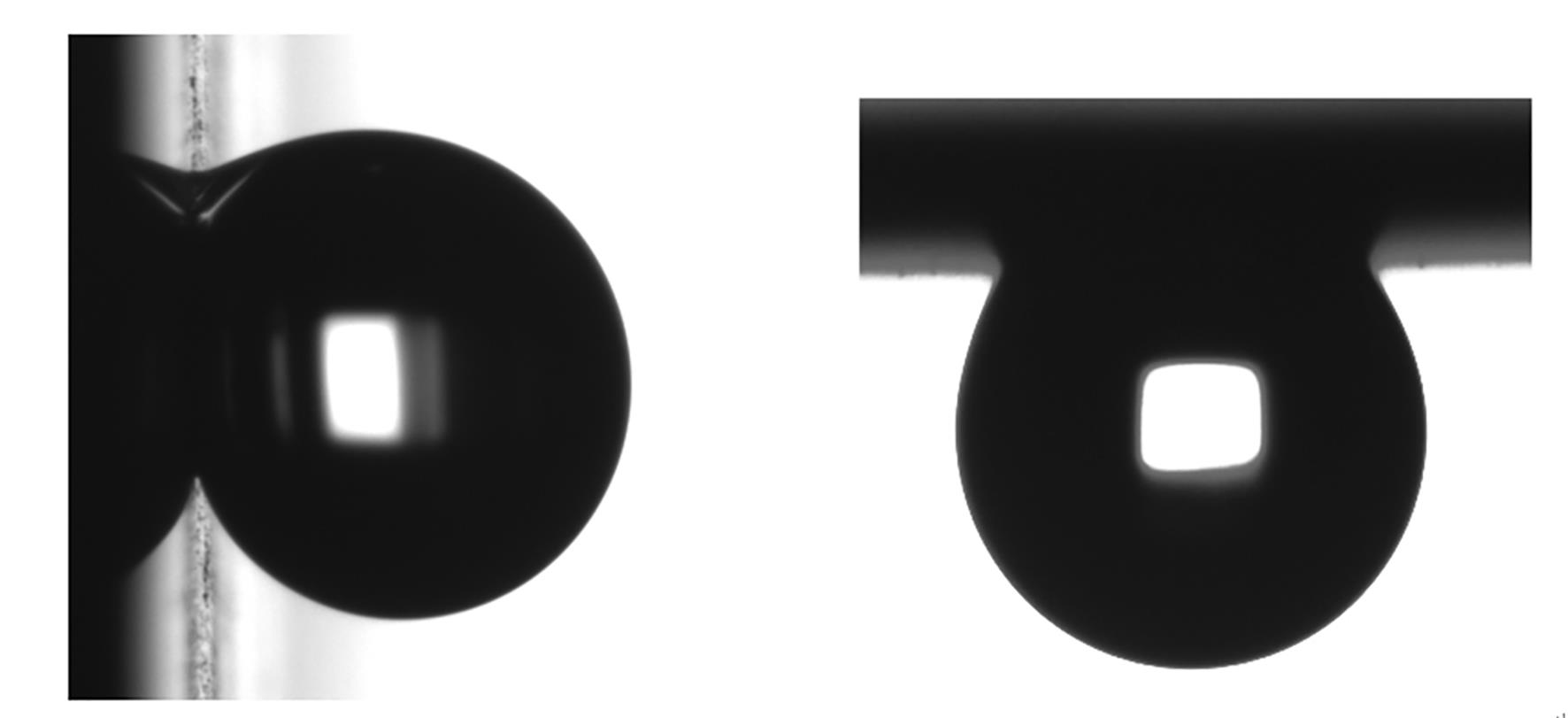
图 10. 图案化铜微纳结构垂直和倒置时水滴的形状
Fig. 10. Shape of droplets when patterned Cu micro-nano structure were vertical and inverted
4 结 论
本文讨论了激光功率、扫描速度和扫描次数对液相下激光烧蚀制备图案化铜微纳结构的影响,分析了激光烧蚀过程中图案化铜微纳结构的形成机制,并验证了该结构在疏水疏油表面材料方面的潜在应用。实验结果表明:在激光功率为2 W,扫描速度为50 mm/s的条件下,随着扫描次数的增加,铜微纳结构呈光斑中心为纳米颗粒,边缘为微米颗粒的铜微纳复合结构,并且结构表面的粗糙度与水/食用油接触角的变化具有良好的一致性,呈现高斯分布。当扫描次数为6时,样品表面水接触角可以达到(155.2±1.5)°,油接触角为(100.0±1.3)°,呈现超疏水和疏油特性。本工作提供了一种简单、廉价、便捷和无粉尘污染的图案化铜微纳复合功能表面的制备方法,这种既具有疏水性又具有黏附性的表面在集水净水系统、微流控和污水处理中有良好的应用前景。
[1] LEO LIU T, KIM C J C J. Repellent surfaces. Turning a surface superrepellent even to completely wetting liquids[J]. Science, 2014, 346(6213): 1096-1100.
[2] DAVIDS P S, KIRSCH J, STARBUCK A, et al. Electrical power generation from moderate-temperature radiative thermal sources[J]. Science, 2020, 367(6484): 1341-1345.
[3] HU C Q, LIU J, WANG J B, et al. New design for highly durable infrared-reflective coatings[J]. Light, Science & Applications, 2018, 7: 17175.
[4] CHOI S, ZHAO Z, ZUO J W, et al. Structural color printing via polymer-assisted photochemical deposition[J]. Light, Science & Applications, 2022, 11(1): 84.
[5] YAMAGUCHI S, OHDAIRA K. Degradation behavior of crystalline silicon solar cells in a cell-level potential-induced degradation test[J]. Solar Energy, 2017, 155: 739-744.
[6] KIM M, KIM T. Cracking-assisted photolithography for mixed-scale patterning and nanofluidic applications[J]. Nature Communications, 2015, 6: 6247.
[7] GEINTS Y E, MININ I V, MININ O V. Talbot photolithography optimization with engineered hybrid metal-dielectric mask: high-contrast and highly-uniform Talbot stripes[J]. Optics & Laser Technology, 2022, 148: 107776.
[8] SHEN L D, FAN M Z, QIU M B, et al. Superhydrophobic nickel coating fabricated by scanning electrodeposition[J]. Applied Surface Science, 2019, 483: 706-712.
[9] WANG Z W, SHEN L D, JIANG W, et al. Superhydrophobic nickel coatings fabricated by scanning electrodeposition on stainless steel formed by selective laser melting[J]. Surface and Coatings Technology, 2019, 377: 124886.
[10] ZHENG J W, YANG J C, CAO W, et al. Fabrication of transparent wear-resistant superhydrophobic SiO2 film via phase separation and chemical vapor deposition methods[J]. Ceramics International, 2022, 48(21): 32143-32151.
[11] FU J G, SUN Y H, et al. Fabrication of robust ceramic based superhydrophobic coating on aluminum substrate via plasma electrolytic oxidation and chemical vapor deposition methods[J]. Journal of Materials Processing Technology, 2022, 306: 117641.
[12] LLOYD R, ABDOLVAND A, SCHMIDT M, et al. Laser-assisted generation of self-assembled microstructures on stainless steel[J]. Applied Physics A, 2008, 93(1): 117-122.
[13] LI J R, XU J K, LIAN Z X, et al. Fabrication of antireflection surfaces with superhydrophobic property for titanium alloy by nanosecond laser irradiation[J]. Optics & Laser Technology, 2020, 126: 106129.
[14] RAJAB F H, LIU Z, LI L. Long term superhydrophobic and hybrid superhydrophobic/superhydrophilic surfaces produced by laser surface micro/nano surface structuring[J]. Applied Surface Science, 2019, 466: 808-821.
[15] SAMANTA A, HUANG W J, CHAUDHRY H, et al. Design of chemical surface treatment for laser-textured metal alloys to achieve extreme wetting behavior[J]. ACS Applied Materials & Interfaces, 2020, 12(15): 18032-18045.
[16]
[17]
[18] WANG H P, GUAN Y C, ZHENG H Y, et al. Controllable fabrication of metallic micro/nano hybrid structuring surface for antireflection by picosecond laser direct writing[J]. Applied Surface Science, 2019, 471: 347-354.
[19] SU Y, WANG S Q, YAO D W, et al. Stand-off fabrication of irregularly shaped, multi-functional hydrophobic and antireflective metal surfaces using femtosecond laser filaments in air[J]. Applied Surface Science, 2019, 494: 1007-1012.
[20] YAN T Y, JI L F, HONG M H. Backside wet etching of sapphire substrate by laser-induced carbothermal reduction[J]. Optics & Laser Technology, 2022, 149: 107900.
[21] ARVI K. Underwater and water-assisted laser processing: part 1—general features, steam cleaning and shock processing[J]. Optics and Lasers in Engineering, 2004, 41(2): 307-327.
[22] YU M M, WENG Z K, HU J, et al. Laser interference additive manufacturing ordered Cu microstructure[J]. Applied Surface Science, 2023, 615: 156312.
[23] ZHANG D S, GOKCE B, SOMMER S, et al. Debris-free rear-side picosecond laser ablation of thin germanium wafers in water with ethanol[J]. Applied Surface Science, 2016, 367: 222-230.
[24] YU M M, WENG Z K, HU J, et al. A Non-enzymatic glucose sensor via uniform copper nanosphere fabricated by two-step method[J]. Optics & Laser Technology, 2021, 144: 107430.
[25] HAN J H, LI Y G, FAN W X, et al. The ablation of Ta2O5 film by pulsed nanosecond Gaussian laser beams[J]. Optik, 2015, 126(20): 2327-2330.
[27] XU Z M, ZHANG Z Y, SUN Q, et al. Effects of nanosecond-pulsed laser milling on the surface properties of Al2O3 ceramics[J]. Coatings, 2022, 12(11): 1687.
[28] ZHANG Z, ZHANG Q L, WANG Q W, et al. Surface microstructuring of single crystalline diamond based on the accumulated energy homogenization in the nanosecond pulsed laser ablation[J]. Optics & Laser Technology, 2021, 138: 106839.
[29] ZHANG D S, SUGIOKA K. Hierarchical microstructures with high spatial frequency laser induced periodic surface structures possessing different orientations created by femtosecond laser ablation of silicon in liquids[J]. Opto-Electronic Advances, 2019, 2(3): 19000201-19000218.
[30] YANG H, XU K C, XU C W, et al. Femtosecond laser fabricated elastomeric superhydrophobic surface with stretching-enhanced water repellency[J]. Nanoscale Research Letters, 2019, 14(1): 1-10.
[31] LIU X Q, BAI B F, CHEN Q D, et al. Etching-assisted femtosecond laser modification of hard materials[J]. Opto-Electronic Advances, 2019, 2(9): 19002101-19002114.
[32] YANG J F, LONG F, WANG R Y, et al. Design of mechanical robust superhydrophobic Cu coatings with excellent corrosion resistance and self-cleaning performance inspired by lotus leaf[J]. Colloids and Surfaces A: Physicochemical and Engineering Aspects, 2021, 627: 127154.
[33] RYU S W, CHOO S, CHOI H J, et al. Replication of rose petal surfaces using a nickel electroforming process and UV nanoimprint lithography[J]. Applied Surface Science, 2014, 322: 57-63.
[34] WENZEL R N. Resistance of solid surfaces to wetting by water[J]. Industrial & Engineering Chemistry, 1936, 28(8): 988-994.
[35] CASSIE A B D, BAXTER S. Wettability of porous surfaces[J]. Transactions of the Faraday Society, 1944, 40: 546.
[36] FENG L, ZHANG Y N, XI J M, et al. Petal effect: a superhydrophobic state with high adhesive force[J]. Langmuir, 2008, 24(8): 4114-4119.
[37] EBERT D, BHUSHAN B. Wear-resistant rose petal-effect surfaces with superhydrophobicity and high droplet adhesion using hydrophobic and hydrophilic nanoparticles[J]. Journal of Colloid and Interface Science, 2012, 384(1): 182-188.
[38] MU H B, WANG Y N, TIAN Y Q, et al. Microstructure and hydrophobic properties of nano-Cu-coated wood-based composites by ultrasonic pretreatment[J]. Applied Sciences, 2020, 10(16): 5448.
[39] LI J, ZHOU Y J, WANG W B, et al. Superhydrophobic copper surface textured by laser for delayed icing phenomenon[J]. Langmuir, 2020, 36(5): 1075-1082.
[40] SHEN X D, ZOU B S, HUANG C W, et al. Femtosecond laser and oscillation induced large-scale periodic micro/nanostructures on copper surfaces[J]. Optics & Laser Technology, 2023, 161: 109166.
[41] WANG D, HU C S, GU J, et al. Bamboo surface coated with polymethylsilsesquioxane/Cu-containing nanoparticles (PMS/CuNP) xerogel for superhydrophobic and anti-mildew performance[J]. Journal of Wood Science, 2020, 66(1): 1-8.
[42] DONG Z L, SUN X Y, KONG D J, et al. Spatial light modulated femtosecond laser ablated durable superhydrophobic copper mesh for oil-water separation and self-cleaning[J]. Surface and Coatings Technology, 2020, 402: 126254.
[43] TONG J W, LIU S S, PENG R T, et al. Development of a micro/nano composite super-hydrophobic silicon surface with nail-shaped texture/dual self-assembly monolayers and its wetting behavior[J]. Applied Surface Science, 2021, 544: 148803.
Article Outline
于苗苗, 翁占坤, 王冠群, 郭川川, 胡俊廷, 王作斌. 液相下激光烧蚀快速制备图案化铜微纳结构[J]. 光学 精密工程, 2023, 31(15): 2248. Miaomiao YU, Zhankun WENG, Guanqun WANG, Chuanchuan GUO, Junting HU, Zuobin WANG. Rapid fabrication of patterned Cu micro-nano structure by laser ablation in liquid[J]. Optics and Precision Engineering, 2023, 31(15): 2248.