非熔透激光搭接焊SUS304奥氏体不锈钢无焊缝侧变形机理
下载: 903次
1 引言
奥氏体镜面不锈钢和镀锌钢薄板连接件常用于家用厨具、电梯和建筑饰板等装饰性结构或建筑中,具有美观、耐腐蚀和经济性高等优点。这些领域对薄板连接件的强度要求较低,但外观要求极高,奥氏体不锈钢镜面上的任何缺陷都会降低消费者对产品的主观评价。常用的此类薄板连接方法有胶接和焊接。胶接相比于焊接,其优点在于连接件无变形,加工难度较低,但胶接的缺点也很明显,如:胶接接头随时间推移老化严重,容易发生胶接件失效[1-3]。非熔透薄板焊接件的优点在于焊接接头质量稳定,并且可以保证无焊缝一侧,即奥氏体不锈钢镜面一侧的表面质量[4-5]。相比于其他焊接方法,非熔透激光焊接的能量更加集中,故焊缝和热影响区更小,焊接变形更小[6-10]。此外,采用激光非熔透焊接的方式焊接镀锌钢与不锈钢薄板时,选择合理的焊接工艺可以有效避免气孔、飞溅和裂纹等缺陷[11-15]。但在奥氏体不锈钢无焊缝一侧,焊缝对应区域会出现表面微凸起变形,尽管此变形尺度十分小,但也会严重影响奥氏体不锈钢镜面一侧的表面质量,这是一个亟待解决的问题。
国内外众多学者对薄板在激光焊接过程中出现的各类变形展开了研究[16-21]。Huang等[16]以固有应变理论为基础,利用壳体模型重现了薄板在激光焊接过程中的失稳变形,并通过相关实验验证了模拟结果。Chakraborty等[17]利用有限元模型分析了激光焊接碗形薄板时板材内部应力和变形的分布,解释了出现焊后弯曲变形的原因。Ai等[18]研究了激光非熔透焊接过程中小孔演变的模型,并以此为基础充分阐明了激光非熔透焊接过程中焊缝的演变和缺陷产生的机制。Choobi等[19]利用自建的人工神经网络模型再现了304不锈钢薄板焊接过程中出现的角变形。孙向伟等[20]利用数值模拟预测了钢板钨极氩弧焊(TIG)时的失稳变形,并辅以三维(3D)光学面扫描测量系统和小孔法验证了数值模拟的结果。刘佳[21]在研究厚度分别为0.8 mm和1.2 mm的301不锈钢板非熔透搭接焊时,结合理论分析与数值计算结果得出了焊接过程中薄板产生的角变形会导致无焊缝一侧发生凸起变形这一结论。当前,国内外研究人员对薄板激光焊接方面的研究主要集中于薄板焊接常出现的角变形和翘曲变形这类大尺度的宏观变形,而对于微凸起变形的研究比较少,且仅限于理论推测,缺乏实验验证。
为了表征微凸起变形的特点,并分析非熔透焊后出现的微凸起变形的机理,本文以激光非熔透薄板焊接实验为基础,研究了激光功率对微凸起变形的影响程度,即对最大变形高度的影响规律。结合反变形法,在不同的反变形量条件下,研究了微凸起变形的变化规律。采用电子背向散射衍射(EBSD)技术分析了微凸起区域的显微组织演变,提出了微凸起变形的变形机理,研究结果对薄板非熔透焊接变形理论与应用具有一定的参考价值。
2 实验材料和方法
2.1 实验材料和设备
激光非熔透搭接焊实验选用表面尺寸为110 mm×110 mm的DC01镀锌钢板和SUS304奥氏体不锈钢板,DC01钢板的厚度为1.2 mm,SUS304钢板的厚度为1.5 mm。SUS304钢板的一面为镜面,另一面为轧制后的原始表面。镜面一侧为不锈钢板使用过程中的工作表面,同时也是激光非熔透焊接过程中需要重点保护的无焊缝一侧。为了对比非熔透焊接时下板SUS304不锈钢的变形特征,并分析微凸起变形的成因,采用相同规格的Q235碳钢与DC01钢板进行激光非熔透搭接实验。实验钢板的化学成分如
表 1. 实验钢板的化学成分
Table 1. Chemical composition of experimental steel plates
|
激光器采用德国IPG公司生产的YLS-10000型光纤激光器。激光焊接零离焦,焦点处光斑的直径约为0.72 mm,焊接时的波长为1070~1080 nm。焊接时采用纯激光焊接的方式,未采用保护气体或其他焊接材料,焊接速率为70 mm·s-1,激光功率为1.9~2.6 kW。
2.2 实验与表征方法
实验所用工装夹具如
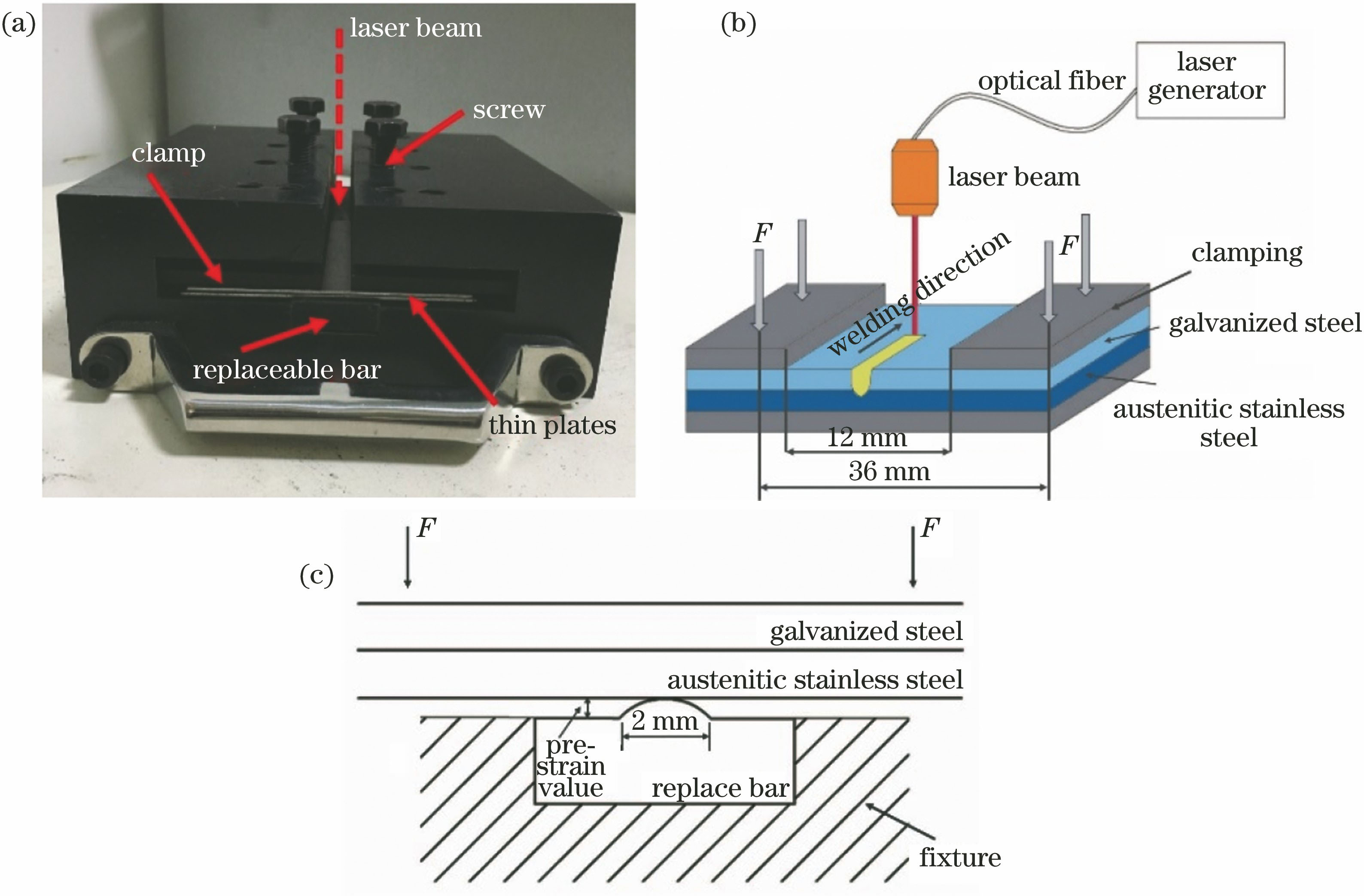
图 1. 激光非熔透焊接实验示意图。(a)焊接夹具实物图;(b)激光非熔透焊接示意图;(c)反变形实验示意图
Fig. 1. Schematics of partial penetration laser welding experiment. (a) Physical map of welding fixture; (b) schematic of partial penetration laser welding; (c) schematic of pre-deformation experiment
采用美国ZYGO公司生产的ZeGage型三维表面轮廓仪测量焊后不锈钢镜面一侧的微凸起变形。轮廓仪将特定波长的激光投射到待测板材表面,接收来自板材表面的反射光,并在计算机中进行处理,从而获得待测材料的表面形貌数据。焊缝截面经磨抛后,用体积分数为4%的硝酸酒精溶液腐蚀,然后利用德国蔡司公司生产的MCK-50MC型金相显微镜观察焊接接头的显微组织。SUS304钢板表面微凸起部位经机械抛光和振动抛光后,利用美国FEI公司生产的型号为NOVA NanoSEM 230的电子显微镜拍摄EBSD图像。
3 实验结果与分析
3.1 非熔透搭接焊缝及其横截面的宏观形貌

图 2. 非熔透激光搭接焊缝与微凸起变形的宏观形貌。(a)焊缝侧;(b)无焊缝侧
Fig. 2. Macro appearances of weld obtained by partial penetration laser lap welding and micro bulging distortion. (a) Weld side; (b) weldless side

图 3. 不同功率下激光非熔透焊焊接接头的横截面形貌。(a) 1.9 kW;(b) 2.0 kW; (c) 2.1 kW;(d) 2.2 kW;(e) 2.3 kW;(f) 2.4 kW;(g) 2.5 kW;(h) 2.6 kW
Fig. 3. Cross-sectional morphology of partial penetration laser welding joint obtained at different laser powers. (a) 1.9 kW; (b) 2.0 kW; (c) 2.1 kW; (d) 2.2 kW; (e) 2.3 kW; (f) 2.4 kW; (g) 2.5 kW; (h) 2.6 kW

图 4. 不同功率下SUS304钢板的熔深
Fig. 4. Penetration depth of SUS304 steel plate at different laser powers
3.2 不同激光功率下的微凸起变形
轮廓仪拍摄到的镜面不锈钢无焊缝区域如

图 5. 不同功率下微凸起变形的3D模型(测量区域宽2 mm)。(a) 镜面区域;(b) 2.4 kW,测量区域宽8 mm;(c) 1.9 kW;(d) 2.0 kW;(e) 2.1 kW;(f) 2.2 kW;(g) 2.3 kW;(h) 2.4 kW;(i) 2.5 kW;(j) 2.6 kW
Fig. 5. Three-dimensional model of micro bulging distortion at different powers( width of measurement area is 2 mm). (a) Mirror region; (b) 2.4 kW, and width of measurement area is 8 mm; (c) 1.9 kW; (d) 2.0 kW; (e) 2.1 kW; (f) 2.2 kW; (g) 2.3 kW; (h) 2.4 kW; (i) 2.5 kW; (j) 2.6 kW
为了更直观地描述该凸起的形貌,从轮廓仪中导出3D轮廓中的一条高度数据,获得不同功率下凸起变形的二维(2D)轮廓,如

图 6. 下板无焊缝侧微凸起变形的2D轮廓。 (a) DC01-SUS304焊接接头;(b) DC01-Q235焊接接头
Fig. 6. Two-dimensional profile of micro bulging distortion of the lower steel plate at weldless side. (a) DC01-SUS304 welding joint; (b) DC01-Q235 welding joint
3.3 反变形法焊后的变形
在不同的反变形量下分别进行激光非熔透搭接焊实验,并测量下板SUS304钢板的最大凸起高度。

图 7. 不同反变形量下SUS304钢板背面的最大凸起变形高度
Fig. 7. Maximum bulging distortion height of SUS304 steel back at different pre-deformation values
3.4 非熔透搭接焊缝背面微凸起处的EBSD分析
为了分析非熔透搭接焊背面微凸起的显微组织,对非熔透侧微凸起处的下板表面进行EBSD表征,取样位置为

图 8. 微凸起区域的EBSD-IPF图。(a)距微凸起变形中心约1.5 mm处的形貌;(b)距微凸起变形中心1 mm处的形貌
Fig. 8. EBSD-IPF images of micro bulging distortion area. (a) Morphology of region about 1.5 mm away from bulging distortion center; (b) morphology of region about 1 mm away from bulging distortion center
3.5 分析与讨论
反变形法是抑制焊接角变形的常用方法[22]。本实验采用的焊接反变形虽与全熔透焊反变形存在一定差异,但仍遵循焊前预制与焊后变形方向相反的变形这一原则。针对非熔透激光搭接焊,在不同的反变形量下,下板SUS304钢板的微凸起变形程度随反变形量增加均得到明显抑制,表明角变形机制是搭接下板非熔透不锈钢表面微凸起变形的重要原因。然而,凸起变形主要集中于变形中心宽2 mm的区域内,通过反变形可明显降低微凸起变形的最大变形量,但并不能完全消除凸起变形的印痕,可见引起非熔透搭接焊下板SUS304奥氏体不锈钢微凸起变形的机制并不仅是角变形。
在实验条件下,如
当向下“挤出”的应力高于SUS304奥氏体不锈钢的屈服强度时,搭接非熔透焊下板SUS304钢板背面便会发生塑性变形而隆起,在焊接试板冷却后保留在表面形成微凸起变形。随着激光功率增大,塑性材料受到的挤压程度越发明显,故微凸起变形越明显。由此可见:下板为SUS304奥氏体不锈钢的搭接非熔透焊缝背面的微凸起变形是在角变形和挤压塑性变形的共同作用下产生的。
4 结论
通过激光非熔透薄板焊接实验、反变形法和碳钢对比实验,以及非熔透下板不锈钢微凸起变形程度和变形区域微观组织的测试与分析,得到以下结论:激光非熔透焊薄板焊接件无焊缝一侧的凸起变形在宏观上表现为平滑的拱形,微凸起主要集中于变形中心宽为2 mm的区域,该中心的凸起区域呈圆弧形;随着激光功率增加,中心凸起区域逐渐增大,并由圆弧形转变成较为尖锐的凸峰。由反变形法实验结果可知:反变形法可对激光非熔透焊薄板焊接件无焊缝一侧的凸起变形起到一定的抑制作用,焊接角变形是微凸起变形的成因之一。同时,非熔透激光搭接焊接件无焊缝一侧的微凸起变形与材料特性有关,下板SUS304奥氏体不锈钢在激光焊接过程中,金属受热膨胀后受到两侧材料的约束并向下挤出形成凸起。SUS304钢板无焊缝侧的微凸起变形是在激光焊接过程中的角变形和热影响区材料挤压塑性变形的共同作用下形成的。
[1] 郑锐, 林建平, 吴倩倩, 等. 结构胶胶接汽车车身金属接头抗环境腐蚀性能研究进展[J]. 材料工程, 2015, 43(3): 98-105.
[2] 游敏, 郑小玲. 连接结构分析[M]. 武汉: 华中科技大学出版社, 2004.
YouM, Zheng XL. Connection structure analysis[M]. Wuhan: Huazhong University of Science and Technology Press, 2004.
[3] 马海全, 王倩妮, 钱雷, 等. 胶接结构破坏模式及失效机理[J]. 失效分析与预防, 2012, 7(3): 162-166.
[4] Wang H Z, Nakanishi M, Kawahito Y. Effects of welding speed on absorption rate in partial and full penetration welding of stainless steel with high brightness and high power laser[J]. Journal of Materials Processing Technology, 2017, 249: 193-201.
[6] 梁行, 阚盈, 姜云禄, 等. 不锈钢薄板激光搭接焊接头的力学性能[J]. 中国激光, 2018, 45(6): 0602001.
[7] 曾强, 朱绍维, 付正鸿. 不同焊接工艺对SUS301L-MT不锈钢接头组织和力学性能的影响[J]. 激光与光电子学进展, 2018, 55(3): 031405.
[8] 周学凯, 米高阳, 刘森, 等. 304不锈钢/T2紫铜超薄板激光搭接焊[J]. 中国激光, 2017, 44(8): 0802006.
[10] 侯志刚. 薄板结构焊接变形的预测与控制[D]. 武汉: 华中科技大学, 2005.
Hou ZG. Prediction and control of welding deformation of sheet structures[D]. Wuhan: Huazhong University of Science and Technology, 2005.
[11] 孟祥海, 李孟星, 吴丽学, 等. 汽车镀锌钢板焊接缺陷分析及对策[J]. 铸造技术, 2018, 39(3): 625-627.
[14] 姬大鹏. 镀锌钢板点焊工艺及焊接缺陷研究[D]. 长沙: 湖南大学, 2012.
Ji DP. Spot welding process of galvanized steel & failure of spot welding research[D]. Changsha: Hunan University, 2012.
[17] Chakraborty S S, Racherla V, Nath A K. Thermo-mechanical finite element study on deformation mechanics during radial scan line laser forming of a bowl shaped surface out of a thin sheet[J]. Journal of Manufacturing Processes, 2018, 31: 593-604.
[20] 孙向伟, 殷咸青, 王江超, 等. 采用三维光学测量技术对薄板焊接失稳变形的分析[J]. 焊接学报, 2013, 34(6): 109-112, 118.
[21] 刘佳. 轨道客车用SUS301L奥氏体不锈钢激光叠焊技术研究[D]. 长春: 长春理工大学, 2012.
LiuJ. Research on laser lap welding technology of SUS301L austenitic stainless steel for railway vehicles[D]. Changchun: Changchun University of Science and Technology, 2012.
[22] 方洪渊. 焊接结构学[M]. 北京: 机械工业出版社, 2008.
Fang HY. Welding structure[M]. Beijing: China Machine Press, 2008.
Article Outline
刘恩泽, 姚成武, 谢雨凌, 张旭东. 非熔透激光搭接焊SUS304奥氏体不锈钢无焊缝侧变形机理[J]. 中国激光, 2019, 46(4): 0402004. Enze Liu, Chengwu Yao, Yuling Xie, Xudong Zhang. Deformation Mechanism of SUS304 Austenitic Stainless Steel at Weldless Side in Partial Penetration Laser Welding[J]. Chinese Journal of Lasers, 2019, 46(4): 0402004.